The Difference Between Thermally and Chemically Produced Safety Glass
A lot of the glass you interact and come into contact with on a day-to-day basis is known as safety glass. This is because this tempered glass allows manufacturers to produce glass that demonstrates significantly higher mechanical resistance, as well as dulled breakage, keeping the people around them safer.
Depending on the need at hand, tempered safety glass can be produced in two main, yet distinct, ways – thermal and chemical tempering.
In this piece, we will be taking a closer look at the process involved for each production method and how they allow manufacturers to supply safety glass for unique environments:
Thermal Tempering
Thermal tempering of annealed glass involves iterative reheating until it becomes malleable, upon which it is immediately cooled. This quenching process is a pivotal stage for developing the characteristic uptick in resistance not seen in annealed glass, and can be up to four times more resistant. Sufficiently rapid cooling cannot be understated in its importance, as it has a causative effect on safety glass resistance – for example, a slow cooling process can produced tempered glass only twice as resilient as its annealed counterpart.
To add, any breakage that occurs once the glass has been thermally tempered will do so in several smooth surfaced pieces, compared to the linear pieces seen in untreated glass. This makes them widely applicable for usage in situations where harm is to be avoided at all costs, such as in showers, entrance and exit doors, windows, store fronts, etc.
Chemical Tempering
With this treatment, an exchange of positively charged ions occur between the glass surface (lithium ions) and the immersion liquid (potassium ions), allowing for the glass surface to change on a chemical level as potassium ions are larger in size than lithium ions, leading to a more compressed and resistant tempered glass solution (five times more than annealed glass).
This chemical tempering is conducted by immersing the glass for approximately 16 hours at 400°C in a potassium nitrate solution, and produces a glass with properties similar to that of thermally tempered glass. The precise control that chemically tempered glass provides makes them ideal for more bespoke solutions, such as in ocular glass or semiconductor technologies.
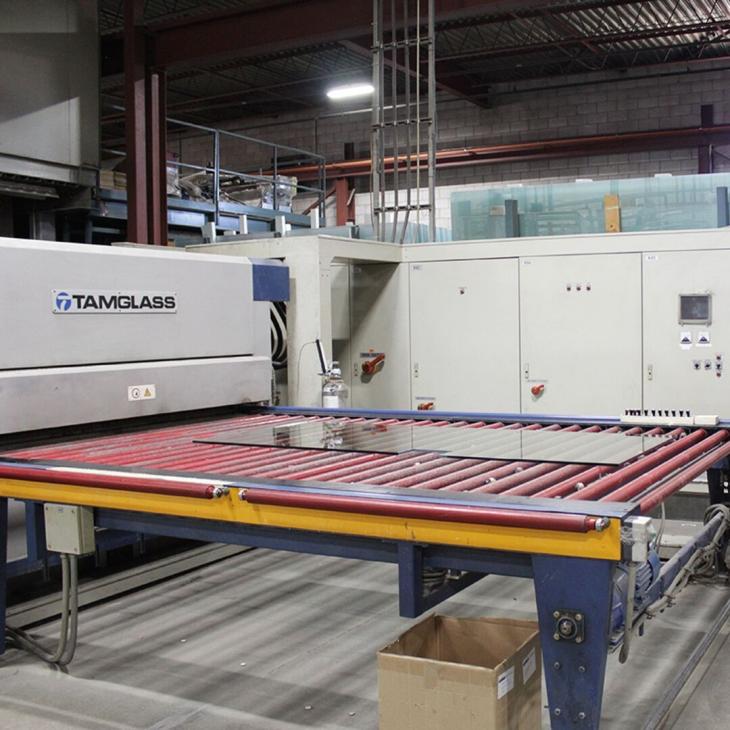
A lot of the glass you interact and come into contact with on a day-to-day basis is known as safety glass. This is because this tempered glass allows manufacturers to produce glass that demonstrates significantly higher mechanical resistance, as well as dulled breakage, keeping the people around them safer.
Depending on the need at hand, tempered safety glass can be produced in two main, yet distinct, ways – thermal and chemical tempering.
In this piece, we will be taking a closer look at the process involved for each production method and how they allow manufacturers to supply safety glass for unique environments:
Thermal Tempering
Thermal tempering of annealed glass involves iterative reheating until it becomes malleable, upon which it is immediately cooled. This quenching process is a pivotal stage for developing the characteristic uptick in resistance not seen in annealed glass, and can be up to four times more resistant. Sufficiently rapid cooling cannot be understated in its importance, as it has a causative effect on safety glass resistance – for example, a slow cooling process can produced tempered glass only twice as resilient as its annealed counterpart.
To add, any breakage that occurs once the glass has been thermally tempered will do so in several smooth surfaced pieces, compared to the linear pieces seen in untreated glass. This makes them widely applicable for usage in situations where harm is to be avoided at all costs, such as in showers, entrance and exit doors, windows, store fronts, etc.
Chemical Tempering
With this treatment, an exchange of positively charged ions occur between the glass surface (lithium ions) and the immersion liquid (potassium ions), allowing for the glass surface to change on a chemical level as potassium ions are larger in size than lithium ions, leading to a more compressed and resistant tempered glass solution (five times more than annealed glass).
This chemical tempering is conducted by immersing the glass for approximately 16 hours at 400°C in a potassium nitrate solution, and produces a glass with properties similar to that of thermally tempered glass. The precise control that chemically tempered glass provides makes them ideal for more bespoke solutions, such as in ocular glass or semiconductor technologies.